Introduction: In the modern and contemporary development of the lighting industry, LED and COB light sources are undoubtedly the two most dazzling pearls. With their unique technological advantages, they jointly promote the progress of the industry.This article will delve into the differences, advantages, and disadvantages between COB light sources and LEDs, explore the opportunities and challenges they face in today's lighting market environment, and their impact on future industry development trends.
PART.01
Packaging Technology: The leap from discrete units to integrated modules
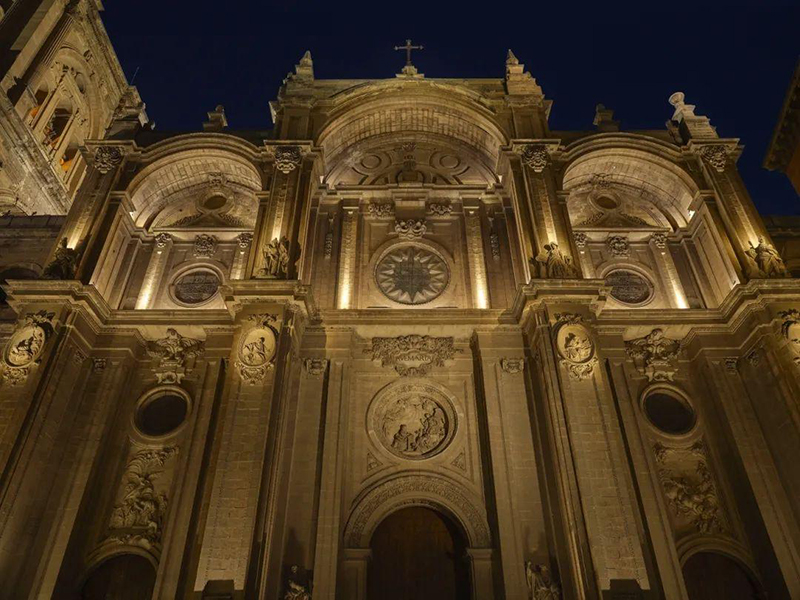
Traditional LED light source
Traditional LED light sources adopt a single-chip packaging mode, consisting of LED chips, gold wires, brackets, fluorescent powders, and packaging colloids. The chip is fixed at the bottom of the reflective cup holder with conductive adhesive, and the gold wire connects the chip electrode to the holder pin. The fluorescent powder is mixed with silicone to cover the surface of the chip for spectral conversion.
This packaging method has created diverse forms such as direct insertion and surface mount, but essentially it is a repeated combination of independent light-emitting units, like scattered pearls that need to be carefully connected in series to shine. However, when constructing a large-scale light source, the complexity of the optical system increases exponentially, just like building a magnificent building that requires a lot of manpower and material resources to assemble and combine each brick and stone.
COB light source
COB light sources break through the traditional packaging paradigm and use multi chip direct bonding technology to directly bond tens to thousands of LED chips onto metal based printed circuit boards or ceramic substrates.The chips are electrically interconnected through high-density wiring, and a uniform luminescent surface is formed by covering the entire silicon gel layer containing fluorescent powder.This architecture is like embedding pearls into a beautiful canvas, eliminating physical gaps between individual LEDs and achieving collaborative design of optics and thermodynamics.
For example, Lumileds LUXION COB uses eutectic soldering technology to integrate 121 0.5W chips on a circular substrate with a diameter of 19mm, with a total power of 60W. The chip spacing is compressed to 0.3mm, and with the help of a special reflective cavity, the uniformity of light distribution exceeds 90%. This integrated packaging not only simplifies the production process, but also creates a new form of "light source as module", providing a revolutionary foundation for lighting design, just like providing pre made exquisite modules for lighting designers, greatly improving the efficiency of design and production.
PART.02
Optical properties: Transformation from point light source to surface light source
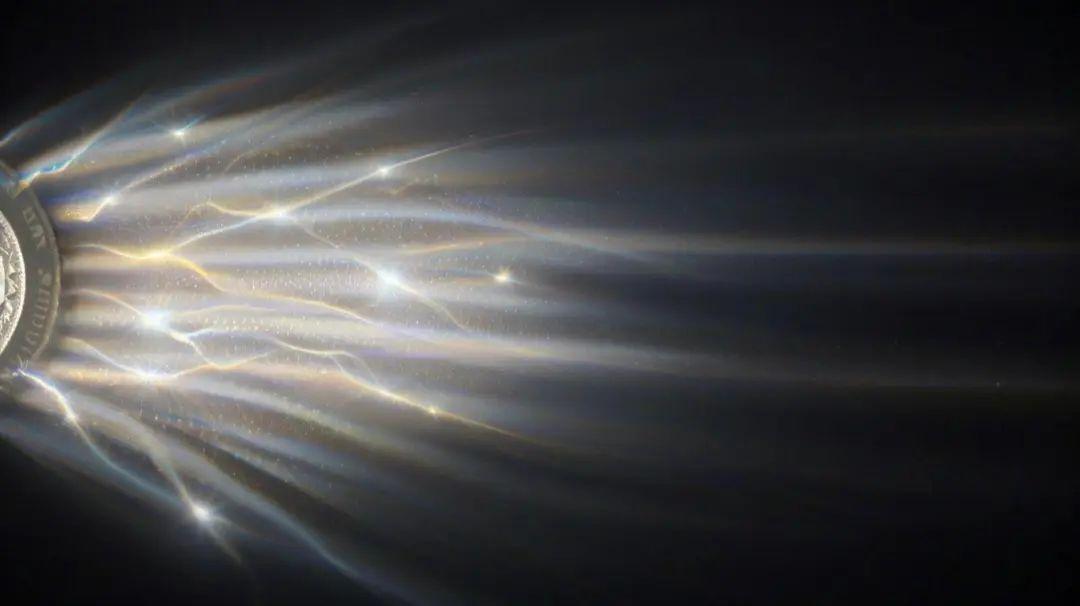
Single LED
A single LED is essentially a Lambertian light source, emitting light at an angle of about 120 °, but the light intensity distribution shows a sharply decreasing bat wing curve at the center, like a brilliant star, shining brightly but somewhat scattered and disorganized. To meet the lighting requirements, it is necessary to reshape the light distribution curve through secondary optical design.
The use of TIR lenses in the lens system can compress the emission angle to 30 °, but the light efficiency loss can reach 15% -20%; The parabolic reflector in the reflector scheme can enhance the central light intensity, but it will produce obvious light spots; When combining multiple LEDs, it is necessary to maintain sufficient spacing to avoid color differences, which can increase the thickness of the lamp. It is like trying to piece together a perfect picture with stars in the night sky, but it is always difficult to avoid defects and shadows.
Integrated Architecture COB
The integrated architecture of COB naturally possesses the characteristics of a surface light source, like a brilliant galaxy with uniform and soft light.Multi chip dense arrangement eliminates dark areas, combined with micro lens array technology, can achieve illumination uniformity>85% within a distance of 5m; By roughening the substrate surface, the emission angle can be extended to 180 °, reducing the glare index (UGR) to below 19; Under the same luminous flux, the optical expansion of COB is reduced by 40% compared to LED arrays, significantly simplifying the light distribution design.In the museum lighting scene, ERCO's COB track lights achieve a 50:1 illumination ratio at a projection distance of 0.5 meters through free-form lenses, perfectly solving the contradiction between uniform illumination and highlighting key points.
PART.03
Thermal management solution: innovation from local heat dissipation to system level heat conduction
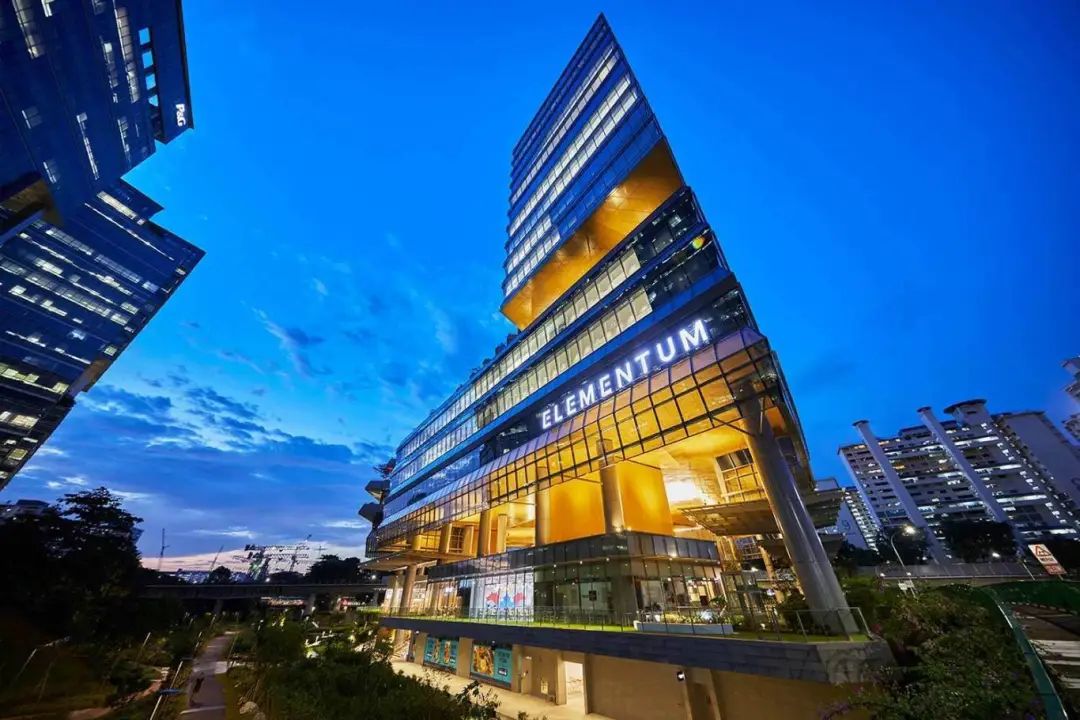
Traditional LED light source
Traditional LEDs adopt a four level thermal conduction path of "chip solid layer support PCB", with complex thermal resistance composition, like a winding path, which hinders the rapid dissipation of heat. In terms of interface thermal resistance, there is a contact thermal resistance of 0.5-1.0 ℃/W between the chip and the bracket; In terms of material thermal resistance, the thermal conductivity of FR-4 board is only 0.3W/m · K, which becomes a bottleneck for heat dissipation; Under the cumulative effect, local hotspots can increase the junction temperature by 20-30 ℃ when multiple LEDs are combined.
Experimental data shows that when the ambient temperature reaches 50 ℃, the light decay rate of SMD LED is three times faster than that of 25 ℃ environment, and the lifespan is shortened to 60% of L70 standard. Just like prolonged exposure to scorching sun, the performance and lifespan of LED light source will be greatly reduced.
COB light source
COB adopts a three-level conduction architecture of "chip substrate heat sink", achieving a leap in thermal management quality, like laying a wide and flat highway for light sources, allowing heat to be quickly conducted and dissipated. In terms of substrate innovation, the thermal conductivity of aluminum substrate reaches 2.0W/m · K, and that of aluminum nitride ceramic substrate reaches 180W/m · K; In terms of uniform heat design, a uniform heat layer is laid under the chip array to control the temperature difference within ± 2 ℃; It is also compatible with liquid cooling, with a heat dissipation capacity of up to 100W/cm ² when the substrate comes into contact with the liquid cooling plate.
In the application of car headlights, the Osram COB light source uses thermoelectric separation design to stabilize the junction temperature below 85 ℃, meeting the reliability requirements of AEC-Q102 automotive standards, with a lifespan of over 50000 hours. Just like driving at high speeds, it can still provide stable and reliable lighting for drivers, ensuring driving safety.
Taken from Lightingchina.com
Post time: Apr-30-2025